Digital twins manage change in E/E design for aerospace
Today’s aerospace projects can incorporate 500km of electrical cabling, accounting for some 3 per cent of body weight. Electrical content has grown 10X in the last half century, ramping more rapidly of late as avionics and other electronic systems have come to play a greater role in design. Innovation, regulation and manufacturing are just three of the sources of additional complexity. Meanwhile, re-use and other grandfathering of existing strategies are often pushed beyond their limits.
As the saying goes, “Change is a constant” – and there is ever more of it.
A technical booklet from Siemens Digital Industries Software describes a methodology that allows design teams and their partners in the supply chain to manage that change in E/E design, leading to better technical outcomes and competitive advantage. It is based on the concept of the digital twin – in fact, it is based three flavors of digital twin: product, production and utilization, with all three connected by a digital thread. This thread allows information to travel both up- and downstream, so that each part of the process informs the others as appropriate (Figure 1).
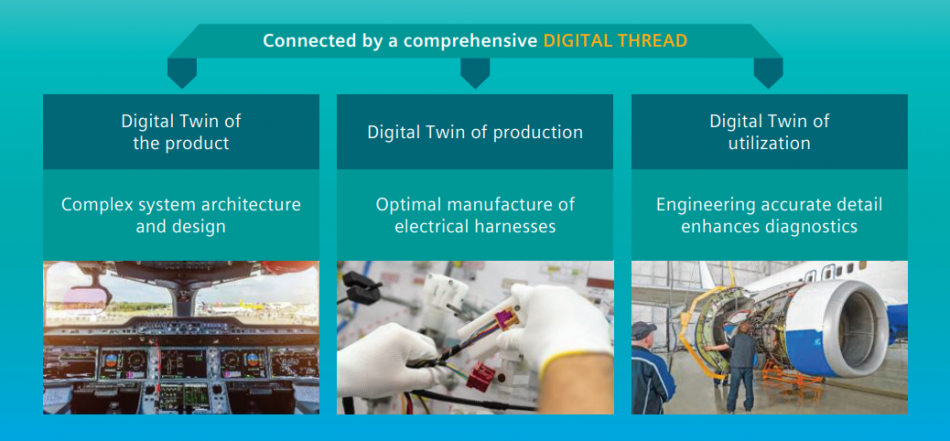
Figure 1. An interconnectedness of digital twin data is made possible via the digital thread (Siemens Digital Industries Software – click to enlarge)
- The product digital twin represents the full digital design representation of the product and its functionality.
- The production digital twin utilizes the digital design and manufacturing process to represent production.
- The utilization digital twin provides the information needed to support the product in service through diagnostics, procedures, component identification, etc.
With specific reference to Siemens’ Capital suite of wire harness software, ‘Managing change in platform electrical systems and turning it into a competitive advantage‘ shows how this process can work by outlining in detail the interplay between these and how the digital thread works across three phases:
“The first phase, known as change assessment, is where change proposal, evaluation and approval occur. This is where a proposed change is prepared and impacts are gathered for multiple areas for technical and financial analysis of feasibility and return on investment.
“Once approved, the next phase is to generate and implement the design change. In this phase engineering implements the change in design and configuration, and then communicates the requirements to manufacturing and the rest of the teams involved.
“The final phase is to implement change downstream and involves many groups including certification, materials, suppliers, and others.”
The aim is to create an efficient configuration-controlled digital twin for E/E systems based around Capital, and it is shown how to achieve this with reference to, in part, the addition of a new satellite communications system.