Overcoming systemic design challenges for electric vehicles
Electric vehicles (EVs) are rapidly coming into the mainstream. Various countries have announced plans to ban internal combustion engine (ICE) and diesel vehicles by 2040. The era of personal mobility and self-driving cars built on electric powertrains is also fast approaching. However, all automakers offering EVs are taking significant losses, mainly due to higher engineering, R&D investment, and electric powertrain costs. How can automakers begin to address these needs and incorporate technologies that meet the wide range of vehicle electrification needs.
By 2040, it’s projected that one-in-three cars sold will be electric. One of the biggest concerns is vehicle range, which must be solved through innovations in battery material and cell development, in addition to electrical vehicle system design. Other vital factors include reducing vehicle weight, improving product lifecycle management, and building powertrain components that have fewer issues with noise and vibration (examples there include electric motors and power electronics as well as batteries).
Safety has always been a major investment for vehicle manufacturers. Electrical vehicles add both more and different safety considerations. Then for autonomous vehicles, no-fail designs are required that can handle increased data network loads and meet enhanced virtual validation requirements. To deliver on safety while innovating to bring electric vehicles into the mainstream, manufacturers must verify and validate the functionality and reliability of the systems that make up a vehicle. Validating these systems requires years, if not decades, of testing in every imaginable environmental condition. Rising to meet such challenges requires sophisticated, intelligent, and collaborative virtual solutions, based on concepts such as the digital twin.
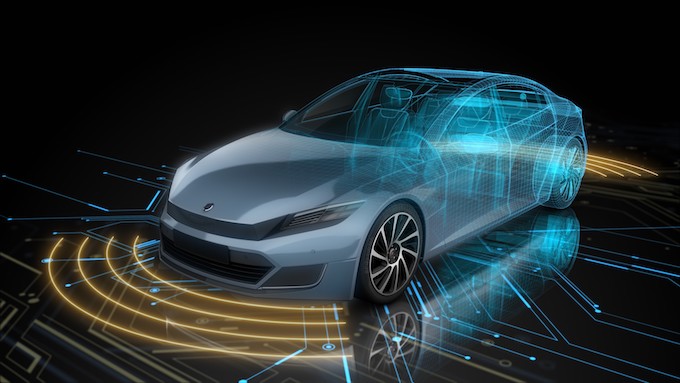
Figure 1. Digital twins are used in EV development, from design to manufacturing to use on the road (Siemens)
Range and charging speed
As the automotive industry gets ready for Auto 2.0, charging time will be central to the customer experience. An adequate driving range for the primary use-case (which will differ for, say, a passenger car against an electric scooters or light duty urban truck), plus fast charging technology, are critical.
For the necessary high-energy battery packs, a current level 1 or 2 charging cycle can last more than eight hours. Therefore, automakers and charging infrastructure companies are investing heavily in fast charging (80% charge in 30 minutes) and ultra-fast charging (80% charge in 15 minutes).
In recent years, state-of-the-art Lithium-ion cells have been at 500-600 Wh/L energy density with a $150-200 /kWh price point. Companies are aiming to develop Lithium-ion cells with an increased cell energy density by around 50%, while reducing cost by around 30%. To accomplish this, OEMs and battery suppliers will need to focus on innovations for new high-energy density chemistry, material optimization to reduce cost, cell and battery pack design, and powertrain optimization to maximize range. Robust cell design and pack thermal management are also fundamental factors for battery safety and durability.
Developing batteries that meet these requirements is extremely challenging. Simulation-driven development – covering battery chemistry optimization, cell and pack design and vehicle integration – can help reduce development time and cost. Accurate software predictions can support the design and verification of an optimal battery pack for any driving scenario and/or weather condition, and help to uncover limiting mechanisms.
Companies must develop and validate optimal charging algorithms and the impact of fast charging on their battery pack life. During charging, if the battery pack or charger temperature exceeds a critical temperature, the vehicle controller will reduce charging speed, lengthening the charging time. Thus, battery pack and faster charger electronics design, algorithms development, and thermal management go hand-in-hand.
Performance and lifetime
Electric vehicle development poses unique challenges and demands balanced engineering to deliver desired performance and comfort without affecting electric drive range and powertrain life. Because the ‘noisy’ ICE engine is absent, noise, vibration and harshness (NVH) issues typically masked in traditional vehicles (from the motor, gear box, and other vehicle sub-systems) become more dominant, affecting design decisions. To meet range and acceleration targets, automakers need to work out battery sizing and explore motor and battery design trade-offs because a higher performance motor can lower the overall cell count for the battery pack, resulting in a better e-powertrain solution.
The in-field reliability of the battery, motor, and power electronics are also major concerns. Maximum temperature and its distribution during in-field operation is a life-limiting stressor for e-powertrain components. Suppliers and OEMs need to account for not only material properties, but also tough-to-measure non-uniform distribution of current, voltage, magnetic flux, and temperature in these components. The performance of one component can impact the flux distribution in another. For example, battery voltage and current affect motor performance because they lead to the generation of more heat.
Multi-domain data exchange between MCAD, ECAD, and CFD software at the early system design concept stage is therefore crucial. Integration and system-level exploits, if left for the later stages, can result in design iterations. These will in turn drive up costs and increase time to market.
For example, the power converter and the electric motor can be optimized separately. A converter/electromagnetic optimization will reduce the converter/motor volume and/or mass to meet the electrical constraints. However, after system integration, the components may fail to meet other requirements such as those for noise, manufacturability, and integration. Even an optimized off-the-shelf solution will only be valid for a certain application and may not relate to other applications. This means that high-performance drives should be analyzed as complete solutions, not only at the component level.
To reduce time to market and cost, both a fast and reasonably accurate system-level analysis and detailed component-level models are necessary. They empower your team in undertaking component design engineering that accounts for upstream system-level implications. Such seamless component to system-level simulation allows companies to explore and exploit potential trade-offs in highly interdependent EV system and vehicle design, reduce design cycles, and ensure the final product is fully optimized.
Electrical architecture
The electrical distribution system is the third heaviest system in a vehicle, after the chassis and powertrain. Reducing its mass contributes significantly to overall vehicle weight targets. Managing the physical size and mass to conduct high currents is one of the more significant challenges facing the design of EV connectors and cables.
One example that OEMs are considering is the removal and/or reduction of high voltage (HV) cable shielding to optimize weight and packaging. One way of achieving this is to manage electromagnetic interference via integrations with tools that analyze the high and low frequency emissions from sources such as HV cables, the battery management system, and power electronics. Evaluating and optimizing cable and harness routing requires tools that are tightly integrated with 3D CAD.
Finally, analyzing the optimal startup/shutdown sequencing of the HV system is now an important consideration. An example of why is the need to support analysis of the HV electrical system capacitance to calculate the correct timing for the system to self-check for welded HV contactors (all EVs run this test on either startup and/or shutdown of the HV system). It is normally a functional safety-driven mitigation action. Also critical is getting confirmation that only the required components in the HV system are woken for the appropriate vehicle modes (e.g., charging mode vs. driving mode).
The Capital portfolio
The Siemens Capital product portfolio supports the electrical systems and network domains. Using a model-based design paradigm, the software can define system architectures and, applying in-built metrics and design rule checks, compare and contrast multiple architectural options to ensure the platform design meets the original intent.
The tools automatically integrate the electrical systems to be incorporated into a representative topological layout of the vehicle. Systems devices are automatically placed and interconnected, and the entire wiring system is automatically generated using rules and constraints that are embedded into the software. Design tasks that took months can now be completed in hours or days with the designs being verified as they are created. Data can be reused across vehicle programs and in downstream manufacturing and service processes.
Siemens EV engineering solutions portfolio enables auto OEMs and key players in the supply chain to develop market-desired vehicles for various segments faster and more profitably. Developing EVs with ranges of more than 200 miles, with fast charge capabilities, in multiple design variants, and for different markets at the same cost of ownership as ICE/diesel vehicles requires innovations and engineering efficiency that has been hitherto unheard of in the automotive industry. At the same time, there can be no compromise on safety, reliability, and quality. For EV development and engineering, various domains (electrical, mechanical, thermal, software and controls) that had either no for few interactions in ICE and diesel vehicles have become strong co-dependent.
Through its domain-specific simulation software offerings underpinned by lifecycle management framework for digital and design continuity from requirements to manufacturing, Siemens offers a digital-twin framework for EV development spanning mechanical, software, electrical engineering, controls, and software domains. With the adoption of Siemens solutions, companies can reduce development time with more accurate and predictable design outcomes, deliver correct-by-construction (data shows 60% less software rework at start of production), lower cost (data shows 40% cost savings in a typical automotive platform), and secure the ability to customize, explore design alternatives as well as adapt to changes easily at every stage of the process.