Welcome to the part model era
A new component digital thread will revolutionize the industry by connecting the nodes of the electronic systems value chain. A digital thread is a communications framework that allows a connected data flow and an integrated view of product data throughout the product life- cycle — spanning ideation, realization, and utilization.
This digital thread simplifies the complexity faced by system design companies and empowers entire cross-functional organizations to go from A to Z with resilience and confidence, unlocking multiple generations of innovation and stimulating growth in profit.
At the founding of the component digital thread is an industry standard, JEDEC JEP30. Ratified in 2018, the JEDEC JEP30 Part Model Guidelines set the stage for this revolutionary phase of the digital transformation within the electronics industry because they effectively define the digital twin for an electronic part.
A digital twin is an essential element of the digital thread, connecting the virtual and physical worlds across the value chain of product, production, and performance. The part model combines component information — that related to the electrical, physical, thermal, and assembly process classification of an electronic part — into a standards-based digital container defined with an XML schema. The part model schema also comprehends standard interfaces and has the flexibility to access specialized models (for example, an IBIS model) that can be added for an applicable device. The standard also extends electrically to support the notion of reference designs associated with the part model of a specific component.
This is a game changer because the JEDEC JEP30 Part Model delivers frictionless value throughout the electronics value chain. For example, the part model can be consumed directly by every tool in the product creation lifecycle.
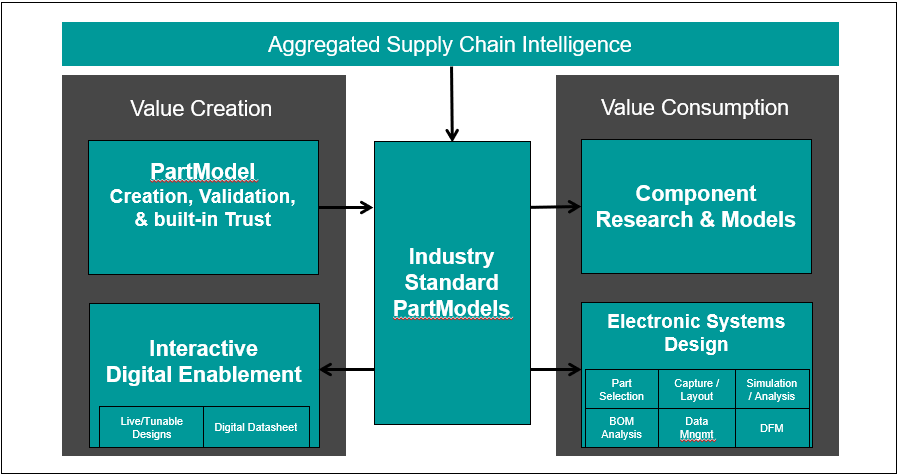
Figure 1. The component digital thread extends value throughout the electronics value chain (Siemens EDA)
The part model era
In the part model era, value creation will shift left to the source: the component manufacturers. As a result, component manufacturers are embracing the JEDEC JEP30 Part Model because it replaces the PDF-based handshake connection between them and their OEM customers with high-bandwidth, intelligent links composed of digital threads. These threads will embed trust and AI-enabled, continuously-updated supply chain intelligence that spans billions of real-time data points related to worldwide electronics part supply, demand, risk, and commercial intent — generating actionable insights that empower better decisions across the entire product lifecycle.
By focusing on digital and standards-based part model containers as the means of exchanging information, the digital thread will accelerate the design-in process and eliminate the human error end-customers unknowingly inject when interpreting PDF files.
Part models are complete digital representations of parts, and many component suppliers are already providing them. Others will follow as more tools are made available to facilitate the transition and validation to the JEDEC JEP30 standard.
For a given part, the component manufacturer represents the single version of truth. As the shift to digital twins of component data accelerates, building in trust of the component information will be a natural expected progression of the standard.
You can therefore envision a day when the part model, and more specifically, different sections of the part model will assimilate digital signatures to establish the basis for an immutable ledger that will initiate trust throughout the downstream design chain. Parts will have a ‘root of trust’ tied to their digital certificates that proves that a given part belongs to that certificate. The certificate proves the component supplier’s identification and certifies that the supplier has completed all the relevant steps to guarantee the integrity of their processes and their supply chain. Similarly, this concept rolls up to the product level. Here, for each assembly, the manufacturer (EMS or OEM) establishes a root of trust that ties to a digital certificate that attests to the integrity of the manufacturing process used for those assemblies. You cannot layer in trust without the digital thread. The digital thread makes it happen.
Derived value at every step
There is so much potential to be realized with the greater digitalization along the electronic systems value chain established by the component digital thread.
As shown in Figure 3, at every stage of product creation, the part model digital twin will deliver derived value directly to the tools used at each step. In action, part models will enable and empower engineers to make better strategic decision-making at every point in the design process. Use of the models will streamline the design process by shortening dependencies because critical information and model content can be derived from the part model. Most importantly, part models powering the design chain process will improve first-pass success rates because they reduce the risks to successful product delivery caused by time delays and human error that accumulate throughout product creation. The digital thread enables this.
The potential benefits are enormous when you add up the time and budget savings made possible during new product introduction. No more searching for model content. No more fixing data integrity errors from a third- party model. No more misinterpreting the numbers in DC and AC switching characteristic tables because it was difficult to decode the naming conventions used by a given component manufacturer. No more needless respins.
Managing electronics today requires a new way of thinking because you need to constantly adapt to the next normal. You do it by empowering your design teams with shifting-left best-of-market supply chain intelligence presented in an engineering context to the point of design. You do it by building systemic cross-functional collaboration within your organization that enables workflows and better cost versus risk trade-off analysis. You do it by shifting from an ‘inside-out’ mindset — an over-reliance on data and information stored in enterprise systems which is notoriously inaccurate and out-of-date — to an ‘outside-in’ mindset that provides actionable insights from across the value chain to every point in technical and business decision-making.
And you do it by having trust in the supply chain. There will now be a digital-thread-enabled traceable process in the supply chain. So, when something goes wrong (e.g., when a part is unreliable or found to be counterfeit) the genealogy of where that part has been used and which products and assemblies might have been affected by a potential malicious action will be available at the touch of a button. This will tailor product recalls to only those products that are directly impacted. Moreover, the OEM can validate the trustworthiness of its product by viewing the digital certificates that guarantee the integrity of the supply chain. The result? OEMs will have assurance and utmost confidence in the quality of the components they use and the products they make.
The technology that makes this happen is the component digital thread. It unites OEMs to the component ecosystem they depend on to bring a successful product to market. It effectively integrates the design chain and supply chain processes within an OEM. This is the next step in the digital transformation that companies are now adopting because it not only adapts to the next normal well, but more importantly, can translate unexpected events into opportunities for growth.
The part model era will enable a digital transformation that will touch all players in the electronics value chain. This is a big ‘T’ transformation because it will revolutionize the electronics industry: it will accelerate the design process, leading to greater profitability; and it will pave the way for new levels of innovation. It will unleash the full potential of your engineering team today.
For an expanded treatment on this topic and the motivations for moving into the component digital thread fueled parts model era, please see the paper Transforming the electronics ecosystem with the component digital thread.