The five pillars of digital transformation for electronics system design
Digitalization unites domains and processes to master the complexity of electronic systems design. Successful strategies share key qualities.
The industry is entering a new era of digital transformation driven by the urgent need for electronic systems companies to overcome three big design challenges— product, organizational, and process complexity.
These challenges are looming larger than ever as companies work to create modern-day, even futuristic, products that weld electrical, mechanical, and software design together — and they have to do so under the strains of shrinking design and production schedules and an unprecedented pace of innovation.
Companies can no longer afford to do things the old way by building multiple prototypes and running them through several test iterations. The traditional prototyping-dependent approach actually contributes to missed schedules, increased development expenses, and degraded product quality.
The negative impacts of not adopting new ways of doing business are significant. Recent research by LifeCycle Insights suggests that 58 per cent of all new product design projects incur unexpected and unbudgeted additional costs and time delays. Only a quarter actually go out on-time and on-budget. To meet schedules, engineering teams often cushion 3-4 respins into their cost and time estimates, thus perpetuating process inefficiencies.
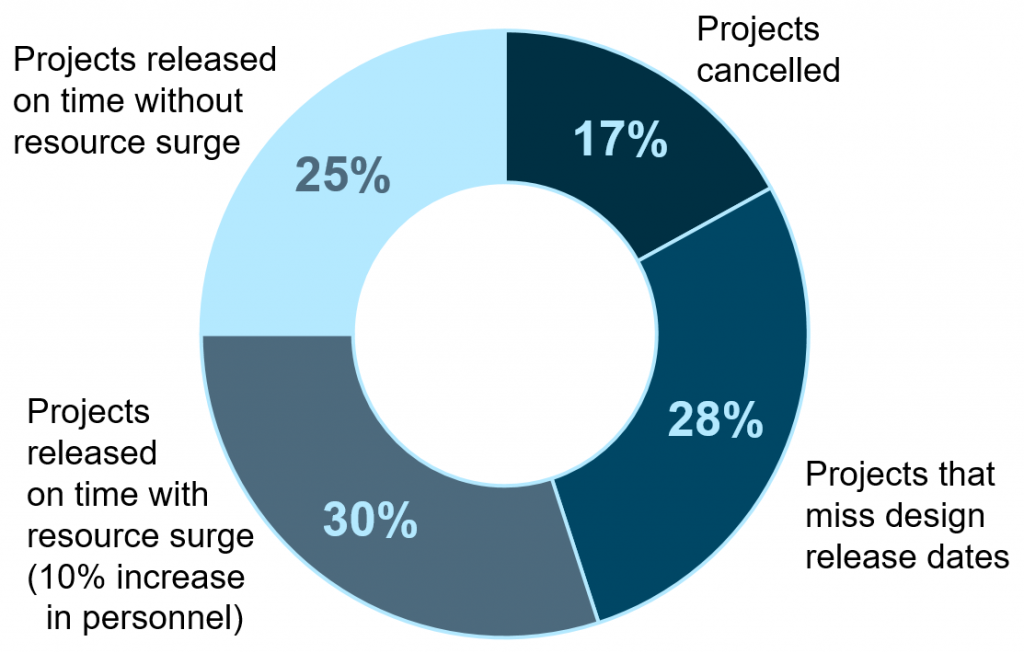
Figure 1. Some 58 per cent of all projects incur additional costs or miss release dates (LifeCycle Insights)
The three facets of complexity
Product complexity has grown significantly with the advent of advanced node ICs, faster DDR memory, and SerDes buses. For example, running signal and power integrity analysis on multi-board designs can be very tricky, and multi-board systems come with difficult connectivity requirements between boards and between boards and mechanical enclosures. Even simpler designs that use the latest generations of FPGA and DDR memory require signal and power integrity analysis. All of this comes at a time of extreme schedule pressure, where the expectation is to get it right the first time, so engineering teams have to get the analysis done quickly and done right. The drive to reduce electronic form factors also drives product complexity, with tighter tolerances between PCBs and enclosures and advanced manufacturing technologies like rigid/flex, HDI, and embedded components.
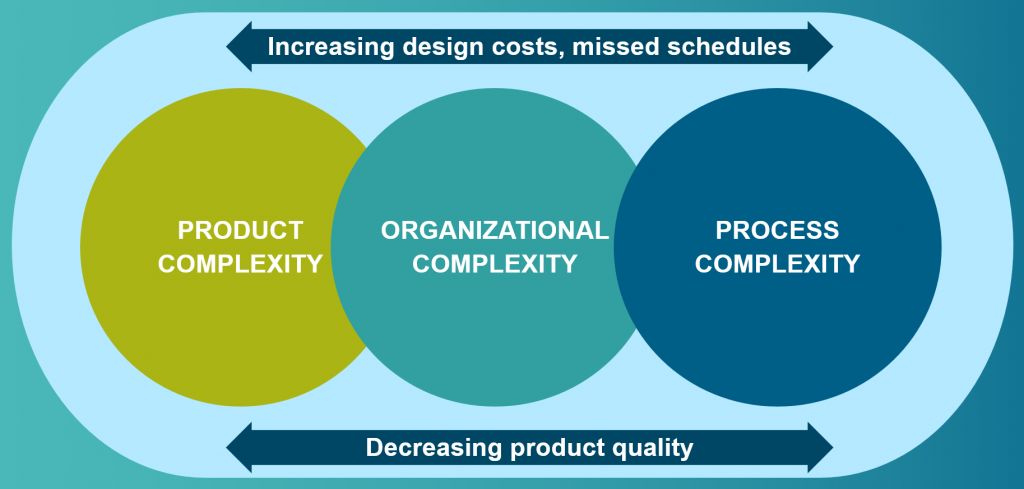
Figure 2. Product, organizational, and process complexity lead to increased costs, lower design quality, and missed schedules (Siemens EDA)
Organizational complexity becomes more entangled as large teams specialize and distributed groups are leveraged to develop a single product. These different design teams often operate independently or in isolation and have poorly defined touch points. Using design tools that cannot share data seamlessly between disciplines often results in problems being found very late in the design cycle or after physical prototypes have been built.
Product and organizational complexities also complicate the core processes throughout the entire development flow — from product concept, to architectural decomposition, through all the multiple parallel domains for electronics, mechanical, and software engineering, and finally to manufacturing. Not only do designs need to meet all their functional requirements; the software that interfaces with the hardware must also work properly. Additionally, all products must meet strict guidelines for their intended operating environments as well as for manufacturability, and in some industries products have to meet a set of complicated regulatory standards.
Investing in the digital transformation
Overcoming these complexities demands a digital transformation strategy that addresses inefficiencies and optimizes both electronic and multi-domain systems design and verification. By embarking on such a digital transformation, companies will break down the barriers between teams, eliminate physical prototypes, and manage IP across the enterprise.
A successful next-generation design platform must support integration, shared data, and improved intelligence. Integration across design processes and disciplines optimizes resources to reduce development time and cost. Sharing context-specific design data reduces design cycles and costs due to fewer data fidelity-driven respins. Improved intelligence provides actionable information and feedback loops to inform cost and resource management decision-making through metrics-driven prescriptive analytics.
In turn, to deliver these three keys to product differentiation, profitability, and beating the competition to market requires five transformational capabilities.
1. Digitally integrated and optimized multi-domain design
Integration throughout design and into manufacturing is essential for producing products that are high quality, low cost, and on time. Establishing a digitally integrated solution across multiple domains reduces manual intervention, fosters collaboration, and improves transparency across disciplines. It enables efficient, secure, concurrent design across all engineering teams, whether individual contributors work at the same site or across the world.
In creating a digital thread between domains, companies establish traceability and interactivity from one domain to the other. Because it gives everyone visibility into product changes, stakeholders can easily monitor status and performance, audit the change history, and review sign-off reports. A digitally integrated solution enables teams to optimize the costs associated with a project, accelerate design time, manage data integrity, and improve the quality of results.
2. Model-based systems engineering
A model-based systems engineering (MBSE) approach from product requirements through manufacturing helps engineering teams solve the multitude of complex and challenging tasks presented by full system design.
It allows team members to view the entire system and model pieces of that system individually higher up the design flow. It does not matter if those pieces are on the electronics side, the electrical side, the mechanical side, or the software side. By looking at the entire system from the MBSE perspective, teams can not only look at the electrical and functional trade-offs sooner, but also better consider product trade-offs that might be based on such things as weight, cost, or even available components.
Then, by leveraging the techniques of MBSE, interfaces can be established towards the beginning of the design cycle between each of the individual domains. In doing so, the implementation within each domain can be isolated from the others. This allows engineering teams to work in parallel, and delivers an early view of the entire product that the team seeks to develop.
3. Digital-prototype-driven verification
By integrating verification throughout the multi-board electronics design process — starting very early, long before physical prototypes — engineering teams can smooth the entire design process and increase design quality through digital-prototype driven, shift-left verification and cross-domain modeling.
Shifting verification to the left in the design flow uses automated, integrated tools, and reduces product schedules to increase the likelihood of an on-time product launch. Cost and time are saved by finding problems early, thereby minimizing design iterations and manufacturing respins. Because a shift-left verification strategy provides efficient, early detection of failures, it is possible to evaluate functional, electrical, thermal, and manufacturability trade-offs when they are easier and cheaper to modify, fix, and compare.
This approach also supports cross-domain digital modeling and simulation without forcing the project to wait until physical prototyping. Instead, digital prototypes drive verification. Given this ability to evaluate alternatives, the cost of the overall system can be greatly reduced.
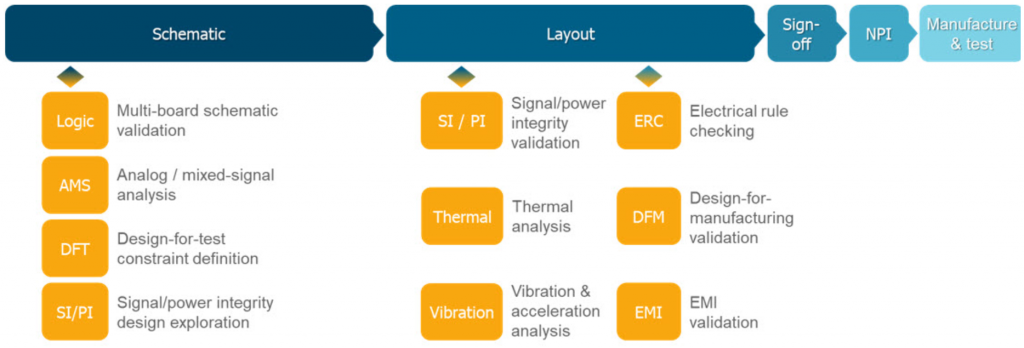
Figure 3. Teams can catch more errors, earlier, by integrating verification throughout the design process (Siemens EDA)
4. Capacity, performance, productivity, and efficiency
Process automation, abstraction, reuse, and scalable tool capacity sustain engineering productivity and process efficiency regardless of design complexity, so design and process complexity will not bog everything down.
A next-generation systems design platform must provide scalability so that it can be tailored to the user’s needs based on an organization’s size, the challenges ahead, and the design team’s expertise. The platform must be able to manage complex designs predictably and reliably including, for example, those with very high numbers of pins, nets, rules, and constraints. The platform it must deliver interactive and automated performance irrespective of design size, complexity, or capacity.
The automation of several key steps throughout the process — from schematic to layout and even verification — will make designers more productive while ensuring they are still in control of the design.
5. Supplier strength and credibility
To facilitate a successful adoption digital transformation, companies need tools backed by a global supplier that can develop, enhance, and support next-generation design platforms.
When selecting a next-generation systems design platform, the natural tendency may be to focus on the solution and the technology behind it. Those are important. But companies should also look at the credentials of the supplier. Are they only a supplier, or are they capable of being a business partner, one that can contribute to your company’s success.
As a part of Siemens Digital Industries Software, Siemens EDA offers an unprecedented depth of mechanical and electronics design and manufacturing execution capabilities. Siemens EDA is currently developing tools, methodologies, and processes that will help your company put these five essential pieces in place, so your organization can turn the promises of the coming digital transformation era into real opportunities today.
The electronics industry is fast approaching a new era of digital transformation. Digital technologies create new business processes, cultures, and customer experiences. They bring together all aspects of product design, including mechanical and electrical. They streamline the entire design process from product inception to manufacturing. To benefit from the digital transformation of electronic systems design, companies need to put in place these five essential capabilities to overcome product, organizational, and process complexity.
For more on how to digitally transform your electronic systems design methodologies and organizations, so you can realize tomorrow’s visions today, read the new paper from Siemens EDA, Raising the pillars of digital transformation for next-generation electronic systems design.
About the author
With more than 30 years of experience, David Wiens has held various engineering, marketing and management positions within the EDA industry. His focus areas have included advanced packaging, high-speed design, routing technology and integrated systems design. He is currently the product manager for the Xpedition Enterprise portfolio of products for electronics systems design at Siemens EDA. He holds a BS in computer science from the University of Kansas.