How MBSE enables advanced E/E architecture design
Model-based systems engineering is a necessary next-step in methodology to cope with the broadening range of innovation across automotive, aerospace and other vehicular markets.
Original equipment manufacturers (OEMs) in the automotive, aerospace and heavy-duty/off-highway industries face common challenges as vehicle technologies converge towards greater levels of autonomy and connectivity. Advanced technologies are expected to improve the safety, productivity and capabilities of passenger cars, aircraft, agricultural and other heavy equipment. Enabling them, however, is driving a rapid increase in the complexity of vehicles in all segments because of the sophisticated electrical, electronic and electro-mechanical systems required.
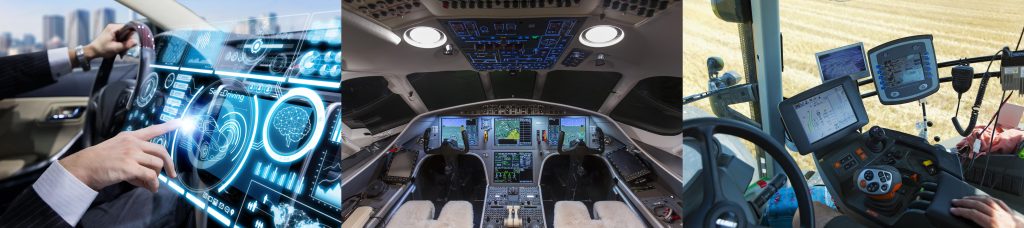
Figure 1. Vehicles in the automotive, aerospace, and heavy-duty off-highway industries are more connected and automated (Mentor)
The result of the continued development of these technologies is an explosion in vehicle complexity across multiple domains. According to conversations with our customers, the typical vehicle in 2020 has 150 million SLOC and 20,000 or more network signals. In addition to more complicated vehicles, OEMs have to manage the lifecycles of all the software, network and electrical components, along with all the other vehicle systems and parts. This involves the coordination of the development cycle to support the launch of the lead program, while ensuring that requirements from other programs have been incorporated.
As OEMs manage the production life cycle of the software and components, they must ensure components are appropriately used in the production and service of each vehicle variant and configured to match each vehicle specification. This involves multiple teams in different parts of the organization. Managing this complexity and ensuring traceability throughout the development process is crucial to bringing advanced, automated and connected vehicles to market on the tight timelines common today.
E/E architecture design in a model-based systems engineering flow
The burgeoning complexity of modern vehicles demands a change in design methodologies. Where traditional strategies relied on manual operations and separated engineering domains into silos, future ones must employ automation and support collaboration through robust data integrity and integrated solutions. Model-based systems engineering (MBSE) offers an advanced portfolio of integrated engineering software solutions, and can provide these crucial capabilities for developing the increasingly sophisticated E/E architectures.
A robust data model is critical to enabling an MBSE flow, where data remains continuous from definition through manufacturing and service. Data continuity allows the work products from each stage of electrical distribution system (EDS), network and software development to be used as input for the next step in the flow (Figure 2). This continuous digital thread of data up and down the development flow enhances the ability of engineers to manage and implement changes as well. The full impact of design changes can be understood before implementation because each domain works from the same digital thread. Once a change is verified, it can be propagated throughout affected domains and designs quickly.
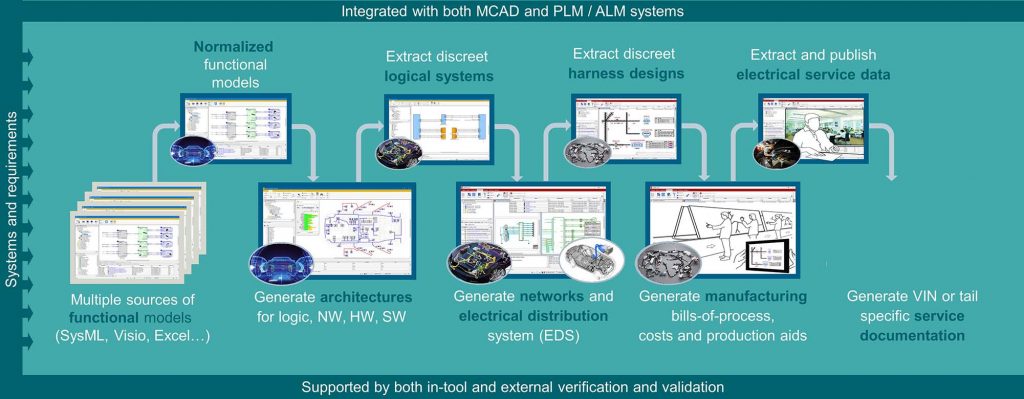
Figure 2. Data continuity enables data from each stage of development to feed the next, ensuring traceability and accelerating development (Mentor)
Furthermore, data continuity provides traceability from functional models to the implementation and documentation of these functions in the vehicle software, networks and EDS. This traceability ensures that engineers can quickly identify the functional source of any component within the vehicle architecture, or, in reverse, find the specific ECUs, networks signals, or pins involved in the implementation of a function.
MBSE enables engineers to leverage existing functional models and engineering data from various environments in the creation of vehicle architectures and more detailed system designs. By continuously building on data from upstream processes, MBSE ensures traceability and streamlines change management and implementation. Many of the processes involved in consolidating models, creating architectures and maintaining traceability are, however, still accomplished manually. Modern E/E systems engineering solutions can improve these processes by automating manual tasks and providing a unified database to ensure data continuity throughout E/E architecture and system design.
Enhancing MBSE for E/E architecture design
Consolidating functional models into a single vehicle platform is currently a manual process that consumes a lot of time and energy. Functional models exist in a variety of different systems engineering tools, each with its own method of abstracting vehicle functionality. Refining just one of these models in a traditional systems-engineering tool to represent its implementation in the vehicle platform with sufficient detail requires extensive manual effort. Multiply this effort across the hundreds or thousands of models usually required to define a vehicle platform and the immense scale of the task becomes clear.
Today, E/E systems engineering solutions can automate much of this work. Instead of adding the necessary domain detail in the systems engineering environment, advanced E/E systems engineering software can import the functional design abstraction. This allows engineers to embellish this abstraction at the platform level with domain details for the software, hardware, networks and EDS. The software then uses rule-based synthesis to deploy functionality in the vehicle platform with the granularity required for subsequent domain-engineering processes.
These specialized E/E engineering solutions also feature built-in metrics for both logical and physical key performance indicators (KPIs), including cost, bandwidth utilization and more. These metrics can drive early optimizations and, coupled with rule-based synthesis, rapid iteration on the E/E architecture. Design rule checks can then identify violations or issues in the physical design abstraction, such as excess bandwidth or ECU utilization.
For example, consider a functional design for a software component that was built in Excel. The E/E engineering solution can import this design, along with the hundreds or thousands of others needed for this vehicle, and deploy the functionality to create a vehicle platform. After deploying functionality, the built-in metrics can show how much RAM is being used per ECU in the architecture allowing engineers to analyze various configurations. Additionally, the engineer can quickly see how much CPU load the current functional allocation will create in each of the ECUs around the architecture, adjusting the allocation if necessary. Once an adjustment is made, the engineer can synthesize an updated architecture, and continue to refine in this manner.
Advanced E/E engineering solutions take this a step further. Integrations with product and application lifecycle management solutions (PLM/ALM), such as Teamcenter and Polarion, allow for the digital thread to extend all the way back to the product configurations, requirements and constraints (Figure 3). This comprehensive traceability ensures that engineers can understand each component or function in the architecture and how it was implemented, but also why it exists in the first place. As a result, vehicle OEMs can produce detailed and accurate compliance documentation automatically, without needing to hunt for information.
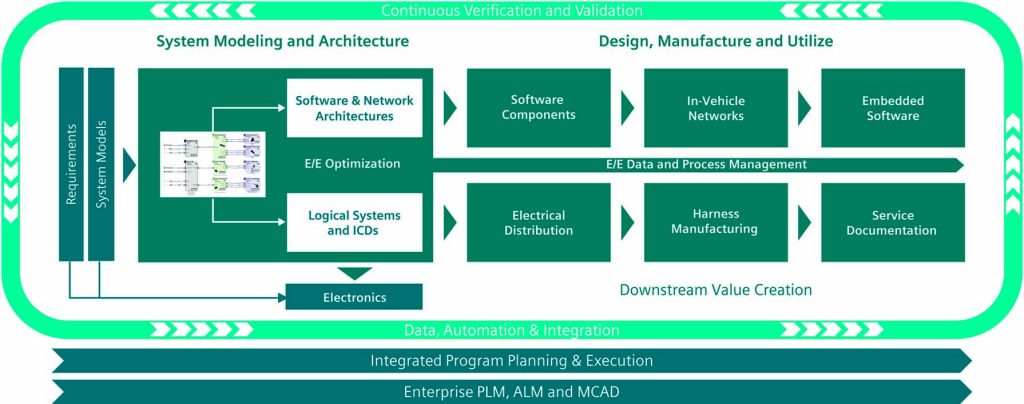
Figure 3. Integrations with ALM and PLM solutions enable the digital thread to extend back to product requirements and definitions (Mentor)
Additionally, the incorporation of embedded software development solutions enables software engineers to collaborate and synchronize with the architectural design directly to develop embedded software application requirements within the context of the system definition. With these requirements, engineers can orchestrate software models and control algorithms, and validate functionality before code is implemented. Software engineers can then leverage automation and contract-based software design to refine the high-level architecture into software components, or they can import existing code for reuse in new vehicle platforms. Meanwhile, an ALM framework tracks software development, provides traceability, coordinates verification and validation, and tracks application configuration and delivery.
MBSE Supports Future E/E Architectures
Vehicles in all sectors are growing in complexity as OEMs develop sophisticated platforms with growing levels of automation and connectivity. In particular, the integration of these technologies is driving a rapid expansion in the size and complexity of vehicle architectures as additional electronics hardware, software applications, networks and other architectural components are required to support the advanced functionality. The complexity of these modern E/E architectures makes them extremely challenging to design and verify using the traditional, labor-intensive procedures that are in place at many manufacturers. In addition, maintaining traceability of vehicle requirements, functions and implementations through each vehicle abstraction becomes nearly impossible.
To cope with the growing complexity of tomorrow’s vehicles, automotive, aerospace and commercial vehicle OEMs must evolve their architectural design processes today to leverage MBSE and the digital thread. Today’s E/E system engineering solutions help companies implement MBSE by providing robust data continuity and advanced automation capabilities. With these solutions, engineers can use existing functional models to generate vehicle architectures and more detailed system designs, continuously building on data from upstream processes to ensure traceability from functions to implementations and actual components or systems. These solutions also provide closed-loop verification and optimization of architectures and system designs to improve vehicle performance at the architecture level.
As vehicles become more automated, the traceability provided by an MBSE flow with advanced E/E engineering tools will only become more crucial as a means of demonstrating regulatory compliance and the safety of a vehicle platform.
Further information
This short video on recent extensions to the Capital E/E Systems Development portfolio and the accompanying description explains how these MBSE techniques can now be brought to the increasingly complex projects discussed in this article.
About the author
Hans-Juergen Mantsch is Technical Director E/E Architecture & MBSE at Mentor, a Siemens Business.