Addressing the challenges of vehicle electrification energy management across multiple systems
A digital-twin based strategy embracing multi-domain, multi-physics simulation can both help control the costs of and accelerate this complex aspect of EV design.
Over 200 models of electric vehicle (EV) are projected to enter the market over the next three years. Most likely, startups will choose new platforms to build their vehicles, whereas OEMs will produce theirs on conventional platforms. As technology continues to evolve and changes the game, there is no clear front runner. The monumental task of building an EV embraces a series of complicated tasks, compromise and patience. Within that context, those with better solutions for energy management will reach higher levels of success and win greater market shares.
The road to electrification runs through hybridization. Hybrid powertrains, though, are more complex than those with a single energy source, such as a conventional vehicle or EV. Engineers must determine which energy source will go to its intended attribute and how the system can be balanced without compromising performance. This involves trade-offs between several physical domains. These include the electrochemical for the battery, the electrical for the electric machines and systems, the mechanical for the transmission, and the thermal for aspects related to the controls.
Model-based system engineering now plays a critical role in managing engineering complexity while controlling time and cost. Among a variety of available applications, multi-domain system modeling and simulation tools bring simplicity to an extremely complex process, allowing for complicated design changes before physical prototypes are created. The earlier decisions are made in the design cycle, the easier and more cost-effective it is to implement necessary changes. System simulation can ensure system continuity, multi-domain traceability and functional safety across domains through virtual validation and verification. This helps with both trade-off analysis and making compromises between attributes. It allows for more efficient integration.
Multi-domain system simulation for fast and efficient optimization
Information-rich and accurate multi-domain simulations that include the battery system, electronics, software, sensors and other key enabling technologies help engineers confront problems early in development. They help them to identify and overcome challenges in the virtual space before costly prototypes are produced. Compared to running testing prototypes, simulation enables the quicker, more efficient and more accurate optimization of processes and devices.
The Renault-Nissan Alliance Group, a leader in the EV market, has been successful in adopting multi-domain system simulation. As a result, engineers in its Test and Digital Engineering department have quickly been able to meet energy consumption targets and run tests in multi-domain system simulation environments. Renault-Nissan uses simulation to ensure it can build the architecture around the needs of the vehicle and optimize the end product based on targets such as size, weight, cost and even technology – all of which impact vehicle cost and energy consumption.
Accurate multi-domain simulation considers a wide range of possible operating conditions and physical effects. System simulation enables designers to move between simulating mechanic, thermal, fluid power, electrical and thermodynamics phenomena (or any other physics of a system) in one virtual environment. Designers can then understand, design and optimize processes and devices for realistic operating conditions. New sophisticated simulation capabilities provide the appropriate multi-level approach to size and the design of all critical components involved in EV architectures, such as the engine, powertrain or battery. Advanced simulation evaluates the complexity of the whole system while addressing thermal and energy management before the project moves to building a physical prototype.
Vehicle energy management is at the crossroads of engineering innovation as it supports understanding performance in the context of an exploding number of systems interactions. It brings a digital twin (Figure 1) approach to solving the inherent engineering challenges coming from the complexity of balancing performance attributes. A digital twin is a virtual representation of a physical product or process to understand and predict the physical counterpart’s performance characteristics.
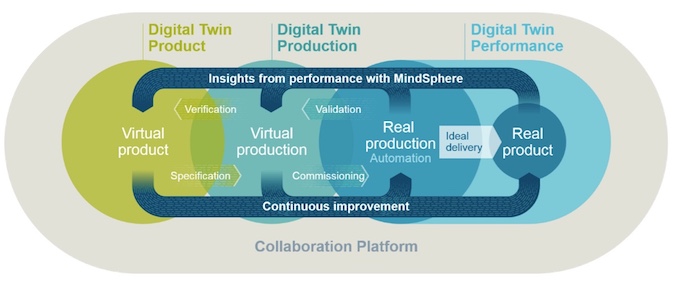
Figure 1. Digital twins are used throughout the product lifecycle to simulate, predict, and optimize the product and production system before investing in physical prototypes and assets (Siemens)
Simulation of subsystem interaction
Successfully designing the overall EV requires that automotive engineers simultaneously address a range of interdependent requirements. Designing an EV powertrain for maximum range and optimal performance is a tough engineering challenge given the complexity of the systems involved (Figure 2). Electric systems and battery designs are evolving rapidly: New materials are being developed, and advanced battery management systems are being implemented that monitor the state-of-charge and the state-of-health of the batteries. To achieve EV architectures that perform to the expected requirements levels in terms of range, drivability, comfort and safety, understanding how subsystems interact is key.
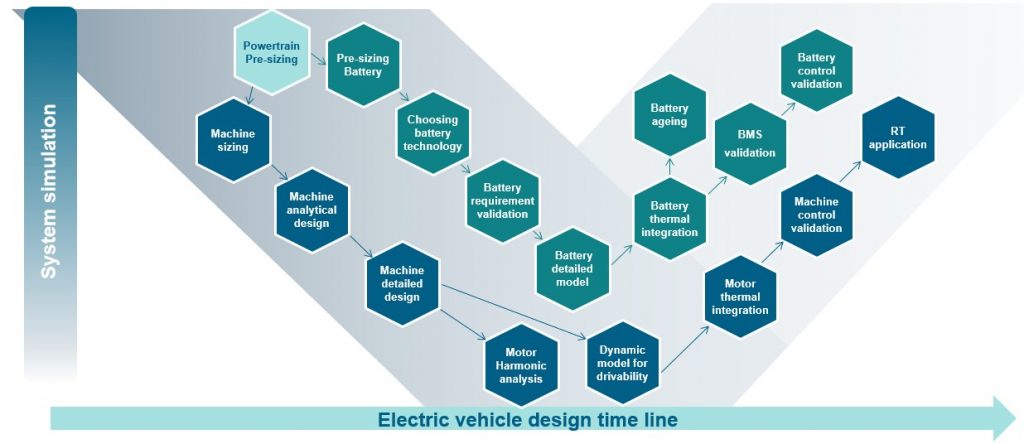
Figure 2: Early systems simulation focuses on sizing and battery technology to determine limitations prior to engineering its systems (Siemens – click to enlarge)
Integrating batteries, electric motors, inverters and generators with all other vehicle sub-systems at the early stages in the design cycle involves capturing data that can be used to determine the global energy distribution and NVH (noise vibration and harshness) performance for balancing attributes. Virtually exploring the performance of any EV configuration is essential to meeting time-to-market and keeping development costs under control.
How can engineers find the perfect compromise between performance attributes that best meets the market’s demands and the regulators’ requirements? All OEMs should ask themselves the following:
- How can you extend range without adding too much weight?
- What is the impact of your architecture on comfort and safety?
- What proper engineering decisions will lead to energy-efficient vehicles that do not sacrifice brand attributes like driving pleasure, safety or power?
Multi-domain and multi-level analysis allows engineers to predict design performance and compare different design variants without the time-consuming and costly process of creating and testing multiple physical models.
Battery system performance optimization
The battery is the most crucial system in an EV, requiring energy management in a different way than a pure internal combustion engine. Battery power can be charged quickly, however, the energy demands and the rate of variation in power delivery are higher because there is no energy source other than the battery. Optimizing battery performance to deliver consistent power without overheating or functional decline is challenging. A multi-physics simulation that considers both electrochemistry and heat transfer properties in a single model can help the engineer find ways to maximize the driving range and lifetime of the battery.
The EV’s battery system must deliver this power repeatedly and without overheating or deteriorating. When the battery is the sole energy source, managing the energy demands and the rate of variation in power delivery are quite demanding tasks. A multi-physics modeling of batteries confronts this challenge by considering both the electrochemistry and the heat transfer properties, then determining where improvement is necessary and how any gains might best be achieved.
For example, starting the car and accelerating cause dramatic spikes. Once the car is up to speed, some battery power can be recovered so the battery current becomes negative. Negative spikes also occur from energy recovery as the car brakes and comes to a stop. Rapid changes in the current drawn from a battery can cause changes in both driving voltage and heating. While a battery can be run at a high-power output (or input) for a short time, it is likely to heat up more quickly at higher current loads. The battery management system must ensure recovery without hindering vehicle power or performance.
Another important influence on EV battery performance is exterior temperature. Extreme hot and cold temperatures impact range. Modern battery systems in EVs are equipped with advanced thermal management systems that can cool the battery when it operates at high loads and heat it when it is plugged in during cold winter nights. Here too, a multi-physics simulation can be extremely effective in determining the best approach to optimizing driving range.
Battery system multi-physics simulation
Recent technologies have increased the power and lifetime of batteries, but they are still a limiting factor in need of performance improvements. Electrochemistry, electric capacity, thermal management, charging control and efficiency are all impacting vehicle level performances. Batteries, from micro-structure chemistry to cell, pack and system design, must be viewed as a whole.
A multi-physics simulation of the battery system can:
- Analyze electrodes and morphology changes at a microstructure level to see how they impact performance;
- Analyze cell performance in realistic conditions and integrate geometry parameters;
- Test the behavior of various cell configurations at the pack level; and
- Correctly size the battery thermal management system ensuring optimal performance during powertrain and vehicle integration.
Multi-level and multi-domain simulation can accelerate battery design and engineering by virtually exploring design variants and assessing multi-level performance. Combining system, 3D and computational fluid dynamics (CFD) simulations allows engineers to easily model various cell chemistry and battery pack designs. They can then evaluate the overall performance in a vehicle context, easily assess battery charging and thermal management processes, and review the best possible control strategies for the highest performance.
Simulation can virtually test SEM-produced electrode geometries, conduct design studies on new concepts and run virtual cell design and tests with detailed geometrical representations. All this can be coupled with a performance model to build a cell digital twin. Engineers can use simulation to run flow, thermal and electrochemistry analysis of complex power systems, and then study the detailed spatial effects at the cell, module and pack levels. Thermal management aspects are also investigated to optimize cooling systems design.
The road to electrification
Vehicle electrification design at the OEM level involves the management of several domains of physics. It also requires the collaboration of different experts at different stages in the design cycle from both inside and outside the EV company.
Innovation requires experts to overcome complexity and manage risks. With cutting-edge simulation technology, engineers can accurately predict product functionality under stress and other various conditions. Multi-physics simulation enables engineers to model EV performance before committing to manufacturing, providing long term benefits for manufacturers by minimizing post-production failures and reducing costs from warranty repairs.
Finally, simulation does not end once the vehicle hits the road. The same models can complement real-life testing as the manufacturer gathers feedback over the lifetime of the EV. Development teams can receive a wealth of continuous data with insight in driver behavior and usage in the field. As this data is added to the overall resource, engineers can use this information to evolve current vehicle simulation models and architectures into yet more efficient, customer-focused EVs.
About the author
Lionel Broglia is a Siemens Digital Industries Software business development manager for system simulation activities in various sectors including automotive and transportation, with a specific focus on electrification. He has been involved in multi-domain system simulation since 1999.