A digital twin methodology to de-risk aerospace electrical design compliance
The digital twin and automation help designers manager increasing aerospace design complexity driven by burgeoning electrification.
Electronic and electrical design demands are creating major challenges for aerospace OEMs. Profitability throught platform development is of the upmost concern. While electrification of modern aircraft is essential, integrating electrical and electronic content brings new levels of uncertainty to platform integration. The concept of the digital twin can play a critical role here.
Historically, platform integration has been dominated by mechanical design processes. With the introduction of electrification, aerospace design complexity is compounding year-over-year. Further, today’s design requirements require interaction across multiple disciplines. These include the electrical, mechanical, electronic, hardware, and software. All of this entails some increase in program risk that can impact the bottom line.
Make no mistake, electrification is here to stay. A recent study by the University of Nottingham in the UK (May 2019), found that increased aircraft differentiation spurs electrification. With more electrification comes greater power demand aboard the aircraft. Figure 1 shows a 25% growth in electric/electrical content every five years and predicts a 10X increase in power demand for commercial aircraft during the next 50 years.
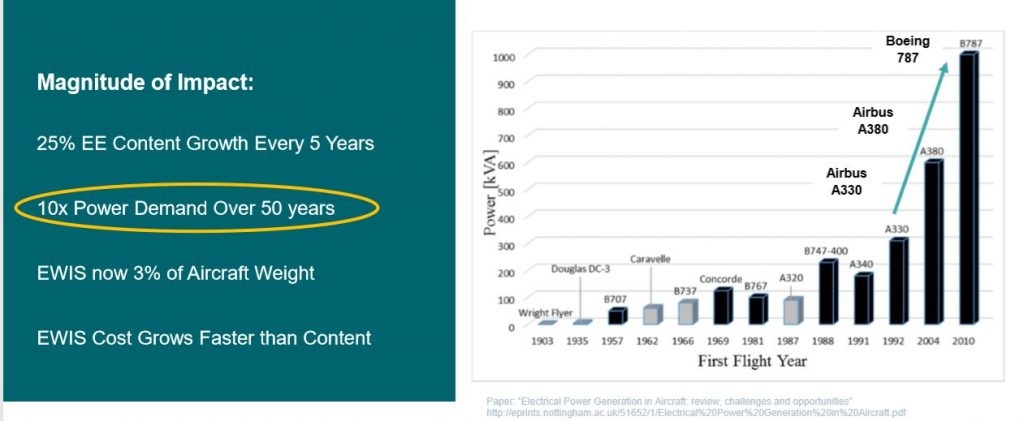
Figure 1. Power generation demand is increasing for commercial aircraft (University of Nottingham – click to enlarge)
Increasing electrical solution functionality
In addition to increased power generation demands, pressures to innovate in and implement electrical solution functionality are having a major impact. This type of functionality includes autoland, in-flight entertainment, passenger USB ports, and interior comfort (lighting, ventilation). Many of these electrical approaches replace mechanical, pneumatic, and hydraulic implementations. Electrical solutions can also increase payload by reducing overall weight of an aircraft (more space for cargo, passengers, fuel efficiency, etc.) thereby lowering energy demand and increasing overall performance reliability.
On a single commercial aircraft, there are thousands of electronic devices/units, miles of electrical wiring, a multitude of configurations to implement, and numerous safety and certifications to consider. Moreover, as electronically enabled functions are introduced in all aspects of product development, they render semi-manual methods and hand-offs from one team to another obsolete, inadequate, and counterproductive.
The rise of the electrical model-based enterprise
Digitalization is transforming the aerospace industry. It is giving rise to the electrical model-based enterprise (MBE) which brings together multiple engineering domains to collaborate up and down the supply chain. MBEs exploit an interconnected and automated value chain, within, and extending beyond, the platform. Stakeholders within the OEM ecosystem employ a digital thread, exploiting digital data continuity, to reference a single model of the platform’s electrical system. The three tenets of a model-based enterprise are discussed in Figure 2.
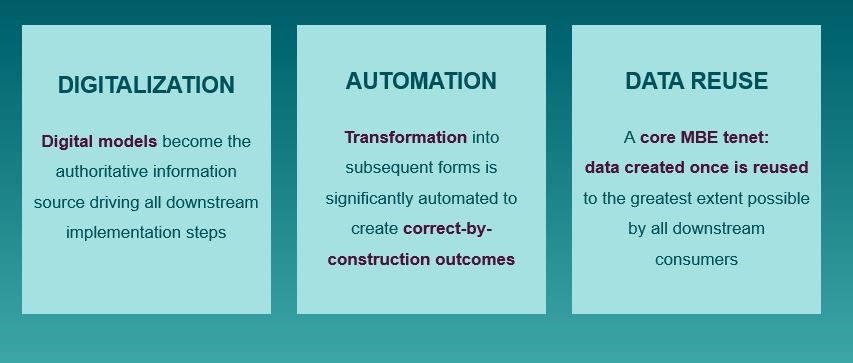
Figure 2. A model-based approach strengthens the value chain for better on-time delivery, higher quality parts, fewer errors, and minimal cost overruns (Mentor)
The bottom line: A model-based approach brings designs, teams, and business functions together, achieving the goal of innovation and higher product quality earlier in the program.
Advantages of the digital twin and the digital thread
A digital twin is a virtual representation of a physical product or business process that can be used to understand and predict outcomes of the physical counterpart. A digital twin can be used throughout the product lifecycle to simulate, predict, and optimize a product or a production system before physical prototypes are created. By applying multi-physics simulation, data analytics, and machine learning, digital twins can demonstrate the impact of many variables. These include design changes, production options, usage scenarios, and environmental conditions. The adoption of a digital-twin methodology reduces the need for multiple physical prototypes and compresses development time.
There are three types of digital twin based on the product lifecycle stage: product, production, and performance that can be combined and integrated (Figure 3). When combined, they form a digital thread by bringing together data from all stages of the design, production and operating lifecycles. This is achieved by employing a software architecture that natively incorporates digital data continuity across the many representations of the product, productions processes, and the operating environment.
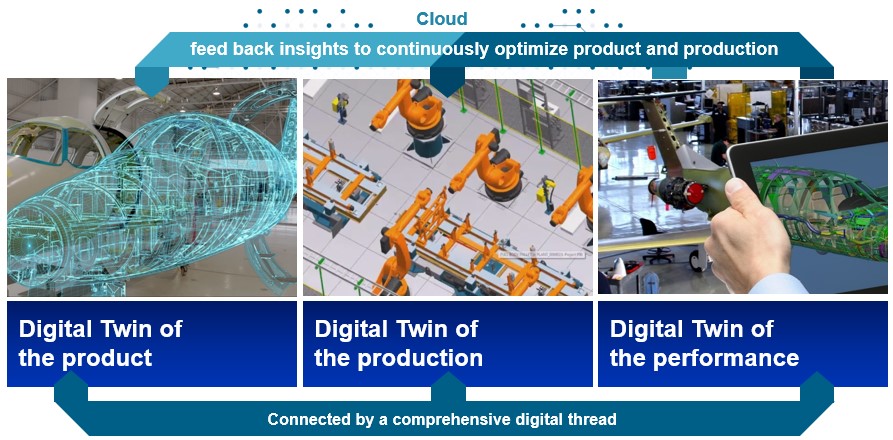
Figure 3. The digital twin of product, production, and performance are connected by the digital thread, bringing data together from all stages of the design, production and operating lifecycles (Mentor – click to enlarge)
The digital twin allows aerospace teams to create, iterate, replicate, and improve their product and process lifecycles, with data coherence and stability, seamless integration, and advanced automation. This helps de-risk and streamline platform electrical design and integration processes. Using a digital twin also provides clear benefits to buyers and service providers of aerospace products since it can provide lifecycle cost analysis and savings, faster maintenance turnaround times, and greater platform operational availability. By leveraging the digital thread (connected product, production and performance digital twins), users can go back to the early stages of design and forward to the platform production, maintenance, and operation with ease. Designers, fabricators, assemblers, suppliers, maintenance, and operators can create a rich, closed-loop environment to make critical decisions and provide continuous optimizations throughout all aspects of the value chain.
Electrification increases – as does compliance risk
As discussed, modern aircraft systems require more power, have more electrical content, and, to complicate matters further, incur higher compliance risk due to increased complexity. To address these challenges, the Capital software suite from Mentor, a Siemens business, now offers Capital Load Analyzer software. This new tool helps simplify aircraft electrical design compliance and certification. It is one of the first electrical systems technologies to leverage automation and digital data continuity to facilitate regulatory compliance.
Employing the electrical digital twin
Current methods for compliance often rely on fragmented data, and are typically conducted manually using drawings and spreadsheets, after major electrical design work is complete. This forces costly design iterations and missed milestones. To mitigate such risks, Capital Load Analyzer draws upon the electrical digital twin, generated from the overall power system and subsystems design, to predict the aircraft’s electrical power demand. The electrical digital twin provides an automated view of the entire power system, enabling engineers to design for compliance from the very start.
Further, Capital Load Analyzer automatically extracts all electrical load analysis data into the user’s reporting template for easy and efficient report generation (Figure 4). This pulls data directly from the digital twin so the user can see the impact of design changes at any time and at any stage of the design. The ability to quickly generate real-time reports enables users to monitor design tasks and identify potential issues early in the design process. This thereby mitigates program risk. Capital Load Analyzer reports compliance analysis results for each design configuration and variant.
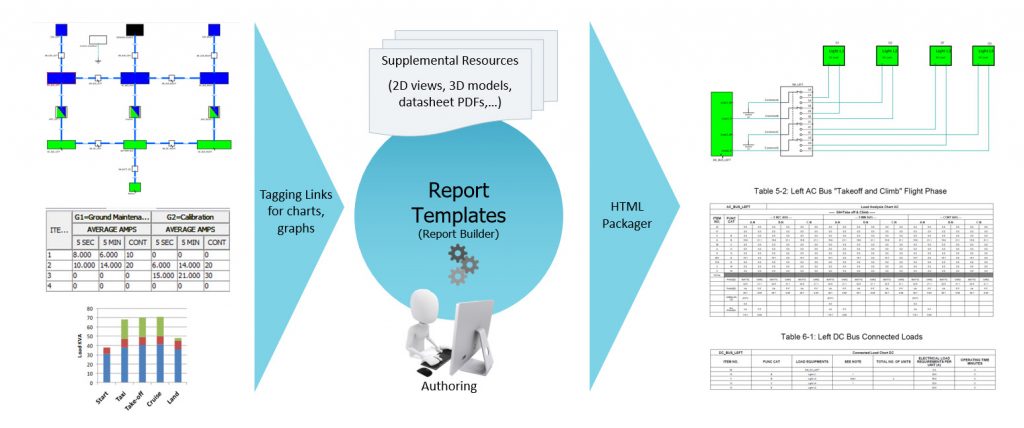
Figure 4: Capital compliance includes integrated reporting that allows groups to populate a report in their own template and automatically refresh it using live designs (Mentor – click to enlarge)
Learn more about Capital Load Analyzer here.
About The Author
Anthony Nicoli leads the aerospace business for the Integrated Electrical Systems Division (IESD) of Mentor, A Siemens Business. Prior to this role, he led Mentor’s technical sales team serving The Boeing Company. Nicoli holds Bachelors and Master’s Degrees in Electrical Engineering from the Massachusetts Institute of Technology and a Master’s in Business Administration from Northeastern University.