A three-phase strategy to master the supply chain tsunami
Supply chain disruptions are wreaking havoc throughout the electronics industry. From component issues to cost increases, it’s becoming more difficult for project engineering teams to design and bring products to market on time and within budget. While project teams are feel this supply chain pain, enterprises face an increased cost of doing business.
We all felt the pain as the Covid-19 supply chain disruptions hit us. I can attest to feeling it firsthand as I had to redo layouts several times over and, in some cases, make design compromises or reductions in final product features to get a project completed and released as soon as possible. I’m not the only one. I recently spoke with my friend and colleague, Chris Young, owner of Young Engineering Services. Chris also writes a column as an industry expert for MilAero007 magazine. He and I recently sat down at a coffee shop in Arizona and exchanged horror stories related to the supply-chain disruption tsunami and its lingering ripple effects.
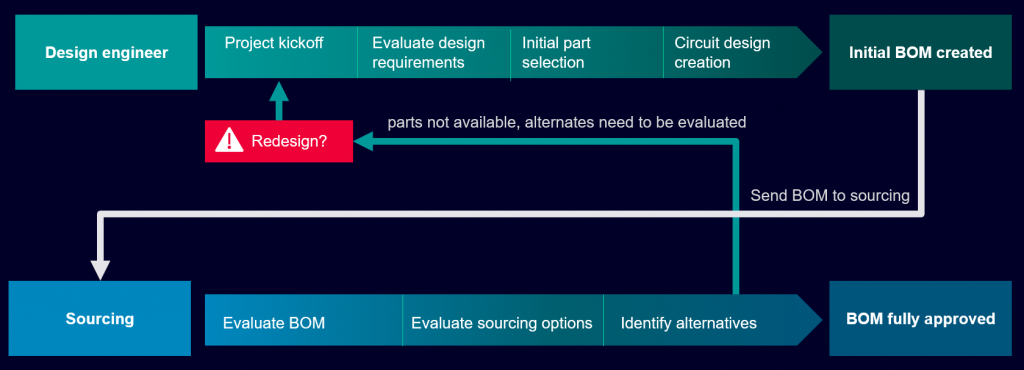
Figure 1. The general design and sourcing process and the impact of supply chain disruption (Siemens Digital Industries Software)
The most shocking revelation for us both was the fact that many component prices and lead times have increased dramatically, with some prices seeing a 100X increase and lead times of more than 52 weeks. Chris and I have written several columns on this topic.
The most recent experience Chris shared with me was an order he placed with a supplier for specific components. The order was taken and input to the suppliers’ systems. He followed up the order with a call to verbally confirm it, and a confirmation number was provided for tracking purposes. A few days later, he received an e-mail notification that his order is now on back order with a ‘TBD’ delivery date. He had been bumped and, as you can imagine, was extremely unhappy. It sent him back to the drawing board to figure out his next move. As I stated, Chris and I are not alone in feeling this pain. The supply-chain disruption tsunami is negatively impacting the entire industry and there is no end in sight.
There are four main categories of rapidly dynamic market forces that continue to stress the global electronics value chain to its limits.
- Electrification across verticals: Today we see increased product complexity as things get smaller and faster, with a big push for many things to go both electric and wireless. Let’s face it, electronics are in everything and there are digital products and services everywhere we look. We’re witnessing a global digital transformation.
- Global supply chain complexity: With today’s globalization, we see distributed teams collaborating and functioning as one complex centralized Numerous suppliers add to this complexity along with ever-expanding geographies.
- Accelerating innovation: As the industry has evolved, so have our engineering tools and This has directly impacted the speed at which we innovate. We see release cycles defined today in months versus years, and these are accomplished with fewer resources on tighter budgets. Adding to this acceleration is heightened competition and customer demand. Product seasonality fuels the speed of innovation. It’s amazing how fast innovation now happens compared to years past.
- Increased supply market volatility: Globalized supply chains are extremely This is due to many years of executing against a ‘just-in-time’ model that is not sustainable with the evolution of today’s industries. Only now has the depth of this fragility exposed due to the pandemic and global geopolitics. There are supply chain shortages in all major industries. We all experience the resulting pain, professionally and personally. Additionally, the lack of data visibility is persistent, making it more difficult to deliver products.
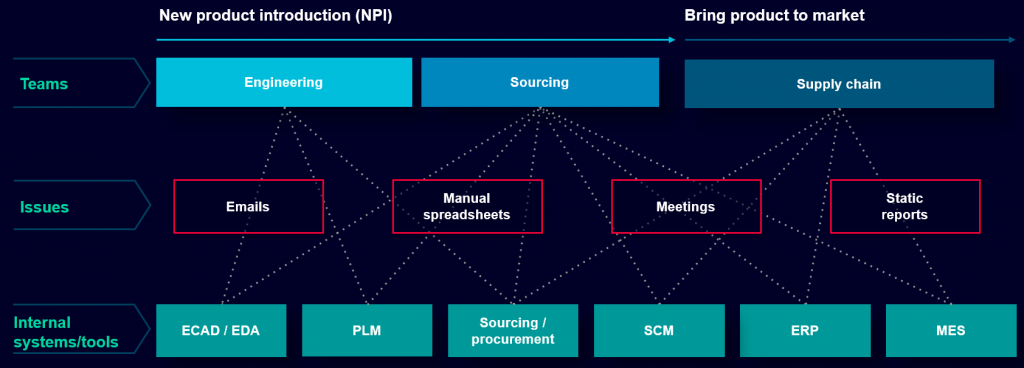
Figure 2. Challenges span functional silos, disparate systems, and fragmented cross-functional decision-making processes (Siemens DIS)
A single solution is needed that is fully integrated with the electronic systems design platform. It must also break through the invisible silos in organizations so better cross-functional decisions can be made. This is particularly needed during new product introductions, when upwards of 80% of life-cycle risks and costs are locked in.
When deployed, this digitally integrated solution will reduce manual intervention. It will foster collaboration. It will improve transparency across disciplines. And it will reduce or eliminate respins between design and manufacturing. Fundamentally, this solution will shift-left real-time component sourcing insights (e.g., cost, availability, life-cycle, compliance).
Additionally, it will deliver performance and electrical parametrics to the engineer’s desktop — allowing more informed decisions at the point of part selection and at the point of design, while enabling seamless collaboration between the engineering and procurement teams. In addition to component sourcing from a host of suppliers, engineers and designers will be presented alternate parts and alerts about component risk, graded at a single-part and BOM level.
With streamlined collaboration between procurement and product development established, the traditional serial handoff process is now concurrent, transparent, and integrated. Fully aligned, design organizations can better manage, adapt, and thrive (competitive advantage) when faced with supply-chain disruptions. Ultimately, designing for supply-chain resilience can have a significant payoff by translating unexpected events into opportunities for growth.
Keys to resilient design
Fortunately, businesses can manage risk and plan for a more resilient future by applying a three-phase solution to enable supply chain resilience for electronic systems design. This promising and effective shift-left approach will transform organizations and expand supply chain resilience to the point of design, allowing companies to optimize not only their systems design process but also every link to the stakeholders in the global electronics value chain.
Designing for supply-chain resilience empowers development organizations and can be implemented with three keys to resilient design. These are deployed in three phases:
- Knowledge: This phase is about arming engineers and teams with comprehensive real-time component sourcing data so they can make more informed part decisions when the cost of change is lowest.
- Intelligence: This phase further applies the insights from component-sourcing knowledge and couples it with part intelligence to empower more informed actions and workflows across the enterprise, lowering cost and This allows the enterprise to adapt quickly to supply disruptions.
- Optimization: This phase delivers a full closed-loop component management digital twin, with built-in traceability, comprehensive manufacturing experiences, and AI-driven analytics, so the optimal choice is made at every point of technical and business decisions.
Recalling the original question: how can businesses manage risk and plan for a more resilient future? The answer: they do it by applying this three-phase solution to enable supply chain resilience for electronic systems design. This promising and effective approach will transform organizations and shift supply-chain resilience to the point of design, allowing companies to optimize not only their systems design process but also every link to stakeholders in the global electronics value chain. By uniting the value chain with the engineer’s desktop, system design companies will see higher levels of digital transformation and the greater profitability that results, as they are empowered to realize, with confidence, the challenges of tomorrow’s designs today.
To read a detailed treatment on the root causes of supply chain disruptions and what your company can do to establish and preserve supply chain resilience, so you can continue to realize your future visions today, please read my latest whitepaper, Supply Chain Resilience for Electronic System Design.