Eight steps for efficient PCB manufacturing and assembly – Part Two
Second in a two-part series, describing critical rules that should underpin PCB manufacturing, and how new technologies overcome increasing complexity.
In the first part of this series, we looked at the first four of the eight crucial steps that will help you achieve truly effective printed circuit board (PCB) manufacturing and assembly. Just to recap, those were:
- Know your product
- Do only what needs to be done – and only when it needs to be done
- Be ready to make anything in any quantity at anytime
- Know exactly what you are doing at each stage in the process
Now let’s take a look at the remaining steps towards achieving success in PCB manufacturing and assembly. These are:
- Stay on top of materials
- Develop efficient exception management
- Ensure assurance, conformance, and compliance
- Deploy seamless operational management
As before, I’ll discuss each in turn, looking at technologies we can use to make them happen.
5. Stay on top of materials
The price of holding excess stocks of raw materials in the factory can rival labor cost differentials in manufacturing in different locations across the world. Issues with PCB materials shortages have progressively shifted from the shopfloor to the warehouse. That does not mean they have been resolved, simply that they have been moved somewhere else.
Relatively frequent stock checks have become essential across the entire factory because significant discrepancies can accumulate between volumes recorded in the ERP system and the physical volume of raw materials held on site. As a result, the minimum stock thresholds set for the warehouse by manufacturing resource planning (MRP) systems are typically higher than necessary. The MRP managers want to ensure there are enough materials to cover any re-order lead times in the additional context of materials that may be ‘lost’ between physical stock checks.
Problems related to material logistics have also spun out of control as raw material volumes have become unmanageable on the shopfloor. There are often partially-used and improperly accounted material reels left around at the end of work-orders. Specific PCB management requirements for materials used in surface mount technology (SMT) processes (e.g., progressive moisture contamination) are often compromised, leading to quality shortfalls.
As a result, customers’ requests for changes to delivery schedules are sometimes deemed impossible to meet because of the high risks associated with the unknowns around physical material availabilities. Then, there is the heavy workload involved in removing and/or reallocating kits of materials.
To regain some control, new tools uniquely identify all materials in the PCB assembly factory using barcodes. These are attached to each material carrier, be it a reel or something else. Each material has assigned attributes that inform advanced stock management and tracking procedures, including support for SMT-specific issues such as the baking and dry storage of materials that are particularly sensitive to moisture. These software solutions enable lean materials management, including Kanban control across multiple warehouses and managed locations on the shop-floor, as well as the proper use and scheduling of just-in-time (JIT) deliveries.
Material selection from the warehouse is optimized for FIFO and many other configurable rules to reduce obsolescence, reduce search, improve location management efficiency, eliminate stock pick mistakes, and offer specialist oversight such as LED bin control. The correct stocks are verified in position on machines at setup to prevent those machines executing with a wrongly located material. Accurate live materials consumption information is synchronized with ERP tools to adjust re-order quantities and ensure the integrity of the inventory.
This eliminates the need for periodic physical stock checks, minimizes machine setup errors, and reduces re-work and quality failures. It also cuts the volume of material stocked both on the shopfloor and in the warehouse while increasing productivity and making it easier to rework production schedules.
6. Develop efficient exception management
Successful PCB manufacturing can be thought of as the creation, one after another, of perfect products. Variation that affects the quality of those finished products threatens that overarching goal.
The PCB test-and-analysis regime has been developed to address defects that occur as a result of production processes gradually or suddenly going out of control. Let’s say, for example, that there is a change in the material supplier. Although the new company may be qualified to supply under a common internal part number, the switch can cause a sudden increase in placement errors if there is just a small difference in, perhaps, height. Machines’ visual detection algorithms can often detect these problems, which is good in terms of reducing placement errors but also results in an ‘invisible’ spoilage of materials at the machine.
Many other problems and defects can slip through manufacturing, only to be discovered at test or even later in the market. Along with material-related issues, process issues around screen printing, SMT mounting accuracy, and reflow can all lead to some degree of variation. The ideal scenario has the test process act as a filter, ensuring that no defective products make it out of the factory. However, the nature of PCB test means that this can never be guaranteed. Statistically, the greater the defect rate found inside the production operation, the greater the corresponding defect rate in the market.
A key factor in reducing defects through test and repair is the speed with which defects are detected and how quickly their prevalence across the factory is determined. Any delay between the defect occurring and being detected increases the likely number of defective units. Several factors determine the time involved. They include:
- Getting the unit into test
- Creating a repair ticket
- Routing the defective unit to a repair station
- Searching for the defect and understanding the cause
- Recognizing the defect
- Qualifying and recording the defect
- Taking corrective action
- Reporting the defect.
Because the consequences can be severe when a major defect is found, typically a PCB line is immediately stopped, pending investigation.
To significantly shorten this process, advanced software can now capture test results and repair tickets electronically, assigning the results to each uniquely identified production unit. Such tools will immediately flag a problem and this ensures the correct routing of a defective unit to the repair station. At the same time, statistical analysis is performed to determine whether a more widespread problem has arisen.
At the repair station, the electronic repair ticket is automatically displayed with the manufacturing and test history and the product design layout data to speed up diagnosis. The software incorporates a statistically-based expert system engine. It can quickly analyze the symptom of the defect on the repair ticket and then diagnose its root causes with reference to previous repairs.
This greatly reduces the time needed to find and process defects, limiting the scope of any quality failure. It also enables the statistical identification of out of control conditions while reducing dependence on specialist skills for defect and root cause analysis. The increased timeliness and accuracy of quality reporting allows the manufacturer to change assembly operations swiftly, thereby reducing the extent of any defects. Fewer defects in the factory means fewer escape into the market.
7. Ensure assurance, conformance, and compliance
There are high costs associated with finding quality issues once a product leaves the factory, especially those that have a safety- or business-critical element. This has led to two key requirements being placed upon PCB manufacturing operations for some time by that last group of customers. Recently these requirements have also been imposed by an increasing number of producers of high volume consumer products.
The first requirement is traceability. Should a defect be found in the market, the supply chain must be able to quickly analyze its source to determine what other units of the same product might have the same problem. In automotive, successful traceability can make the difference between recalling thousands of cars and a more controlled scenario where only a few hundred cars are recalled.
The second requirement is conformance to designated operational standards. This is an attempt to reduce defects by making every operation follow a defined procedure. Conformance strategies will likely have built-in checks that ensure that everything is performed correctly, in the right sequence, and with the right setup.
Unfortunately, both requirements usually increase PCB manufacturing costs because they require additional human input, both to enforce compliance and to record processes. They can reduce productivity as they add additional tasks and force temporary pauses in a line for manual data collection. A lack of confidence in any manufacturing process can lead to the imposition of crippling procedures.
To promote compliance without impeding the PCB manufacturing flow, new software-driven approaches continuously gather data about materials and processes during operation. The data includes test results, the movement of units through production, materials placement and more. Almost all this information is collected automatically and associated directly with each specific production unit. The tools then generate complete traceability build records.
The software follows best practices. It enforces and checks correct operation as part of the standard process. For example, it will verify the presence and composition of materials at the time of machine setup.
Traceability is achieved at minimal additional product cost or effort because it becomes a built-in part of the whole PCB manufacturing flow, not just the SMT machines. Automated analysis and reporting functions can build records on demand, so that any issue can be quantified and contained at a moment’s notice.
Conformance and traceability reduce the number of needless product recalls, enforce quality and control costs. Moreover, the cost of ownership and operation for these tools are minor compared to processes that require manual data collection. In fact, when they are used effectively, these tools often deliver instead significant operational benefits.
8. Seamless operational management
Because of the complexity of SMT-based PCB manufacturing, different teams must assume different roles across the flow, each with different motivations and incentives. The performance of each team is measured in different ways. This can lead to boundaries (or, commonly, ‘silos’) being erected between various competencies, and a situation where operators, engineers and managers may work well within their own specialities but do so far less efficiently at the boundaries of their responsibilities.
For SMT, specific competences that can become silos include production operation, production management, planning, supply-chain, quality, and industrial engineering. When an issues arises, each team may well have a different perspective, often leading it into conflict with colleagues elsewhere.
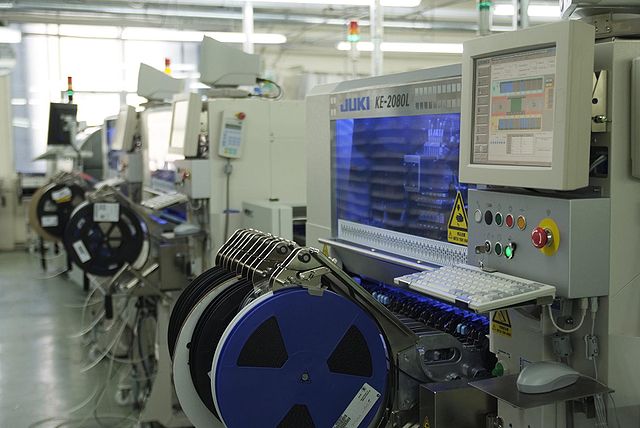
The complexity of SMT-led PCB manufacturing requires teams with varying competences (Source: Megger)
As a result, some problems can go unaddressed because a solution is perceived to entail more cost than simply ‘letting it go’. Initiatives within or from one team may have detrimental effects on others, and come to be seen as little more than ‘flavor of the month’ improvements. They can also quickly lose their attraction once attention becomes focused elsewhere. This limits real improvement and results in far too many missed opportunities.
In a manufacturing environment built around a common PCB manufacturing software infrastructure, everyone has a consistent view. Diverse information from different parts of the operation is qualified, accurate, and timely. Everyone gets the same information from the same source, but tailored according to each particular group’s competences. This enables different teams to work more effectively together, avoiding differences of opinion. Everyone can work toward a successful conclusion.
Benefits include higher productivity and better quality. Responsiveness is more timely, fixes stay fixed, and a much more harmonious shop-floor working environment is created. For example, as delivery timetables change, planning changes can be made and executed by each team within a context that makes them part of their normal workflow.
Conclusion
The challenges that PCB manufacturing faces are not new. However, the complexity of today’s products and manufacturing processes mean that they can be much greater in both their scale and impact. That highlights a now compelling need for change.
Volatility in customer demand is an inevitable by-product of consumers’ increasing influence on the high technology economy, and also our need for more energy-efficient devices. In addition to their complexity, today’s ‘core’ products actually tend to have many more variants and shorter life-cycles. All this requires that factories adopt a step-change improvement in the flexibility of their operations.
Most volatility is due to a distribution chain where the elimination of buffer stocks has propagated lurches in demand right through from consumers and commercial customers to the factory floor. A complete manufacturing operation needs to be re-engineered to enable it to efficiently react whenever timetables and product mixes change as a consequence of end-market turbulence.
In response, automation within SMT manufacturing is now extending from the machine and mechanical level into software. The complexity inherent in SMT technology is too great to manage manually. It must be automated with regard to key data. Today’s advanced software capabilities provide a unique combination of support for the key areas, providing automated control mechanisms as well as a higher order of information for management purposes.
About the author
Michael Ford is Senior Marketing Development Manager in the Valor Division of Mentor Graphics.
Having majored in Electronics, Michael started his career with Sony, gaining a combination of hardware, software, system architecture and manufacturing skills, leading to the creation and management of Sony’s global Lean Manufacturing solutions in Japan.
Since joining Mentor Graphics in 2008, Michael has become a key contributor to thought leadership in the industry, predicting trends and bringing insights on opportunities that can be gained by customers, driving the evolution of manufacturing execution technologies to deliver direct business benefits.
Part One of this article can be accessed here.