Wright on target
We are given plenty of reasons why we ‘should’ all buy electric cars. They will safeguard the environment. They will enhance national security by reducing our dependence on foreign oil. They will create a Detroit 2.0 that can pay back the taxpayer. What we do not hear is a more free-market economic argument.
“And the reason for that is because it fails,” says entrepreneur Ian Wright. “The fundamental problem is that you’re competing with the Toyota Camry, the best-selling mid-size car in the U.S. For less than $20,000, it does more than 30mpg. You can buy one and be sure that you’ll get 50,000 miles out of it and it’ll be reliable. The way things are today, an electric car is going to be $50,000—and that still might be subsidized. The number of people willing to pay that kind of premium is vanishingly small.”
Credit: Scott Beale
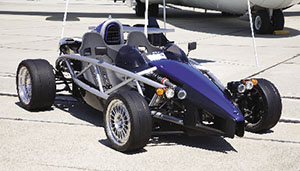
FIGURE 1 The Wrightspeed X-1 can go from 0-60mph in less than three seconds
Wright is the CEO of Wrightspeed, and what is a bit counterintuitive here is that he is in the electric car business. A veteran of Tesla Motors, Wright’s own venture has already delivered a prototype, the X-1, that has outstripped many traditional ultra-high-performance cars going from 0-60mph in less than three seconds. He is also now talking to some large clients for his electrical vehicle (EV) technology. So, he is not trying to talk down his market here—rather, he thinks that it is being approached in the wrong way.
“How is it that so many companies are trying to build electric family and city cars?” he asks. “My theory is that the execs had a room full of engineers and they tossed out the wrong question. They said, ‘How can we make our vehicles more efficient?’ And the engineers thought, ‘OK, so what’s our most efficient vehicle, and how do we take, say, the [Toyota] Prius from 50mpg to 100?’ And that’s still wrong. Because what they should have been asking is, ‘How do you save the most fuel?’”
This is not just about conserving resources. Wright makes an argument that does come down to cold, hard cash—economics, but from a different perspective. “If you look at where all the fuel is going, the biggest selling vehicle in the U.S. last year was the Ford F-Series pick-up truck. It’s been that every year for the last 25 years, and in fact, three of the top five cars are the big, full-size pick-ups. Now, if you take one of those trucks getting 10mpg and improve it to just 11.2mpg over 15,000 miles a year, you’re going to save more fuel than you do by taking a Prius from 50mpg to 100mpg over 15,000 miles. Just go and do the arithmetic, it’s very simple.”
Indeed it is, and the numbers Wright offers represent fairly typical usage. But what matters more is that the transition from family to more heavy-duty vehicles also points the way toward the EV’s holy grail: a three-year payback to the buyer.
Again, taking the example of a mid-size car, the actual window of opportunity for electric drive is very small. Driving such a vehicle in congested traffic for about 10 hours a week—a pretty standard commuter experience—will consume about 150 gallons a year. At today’s $3 per gallon gas price, that means the wiggle room for an EV is about $450 a year, $1,350 over that three-year rule-of-thumb. So even though the Chevy Volt has been pitched at a net price of $32.500 ($40,000 dealer before a federal subsidy), it’s still some way off the $20,000 Camry. “You don’t cross the chasm,” says Wright.
But there is another model available in the shape of the stepvans used by delivery companies. “We’ve found that if we build our powertrain for an electric mid-size car it would cost x dollars and you can see the savings you get. Now, if we build the powertrain for one of those delivery trucks, it costs more, about 2x, but the fuel savings are 10x because those things are burning three to four thousand gallons a year, and we can save almost all of it,” says Wright. “You get that three-year payback.”
Wright acknowledges that even these numbers may not be exactly in place just yet, and one of the big obstacles is the batteries. “If you look at the good batteries—and you’ve got to use those for the reliability, for the recharge time, for the cycles—it’s about $1,000 a kWh, albeit with a reasonable projection of $500 in the foreseeable future, and once we get there you can get your payback. And if the price goes above $3 a gallon, then you’re saving a lot of money,” he says. “Here’s another way of looking at it. Say you reach $550 a kWh for the batteries, you have a 20kWh battery pack and a vehicle that uses 600Wh per mile. That’s a good stepvan profile. OK, so the same vehicle used to do 8mpg. If it does 125 miles a day, with a cost of capital at 5% per year, then you get the three-year payback and a really big return at five years.”
Perhaps equally important, there is a potential here not only to build new vehicles but also for retrofits. Many of these vans have new powertrains fitted, so Wrightspeed could get into the market and start generating sales relatively quickly.
This is all a long way from the cool X-1 racer with which Wrightspeed made a splash almost four years ago. Wright himself admits that in commercializing its technology, the company will have to “change pretty much everything.” However, he has not given up on the high-performance market for the water-carriers.
“One thing to remember about electric drive is that it breaks the 100-year tradition that we have to trade off performance and efficiency,” he says. “If you build in conventional powertrains, then if you want to be efficient, it’s going to be slow. If you want high performance, it’s going to be thirsty. And there really isn’t any way ‘round that. With an electric car that isn’t the case. So, here’s a comparison. If you take the McLaren F1 [supercar], it has similar performance to the X1, but the best you’re going to get out of it is 12mpg. Now, if you drive the X1 on the EPA combined cycle [used in the U.S. to formally rate gas usage] you get the equivalent of 170mpg.”
The massive efficiencies possible with EVs have long been recognized. In a piston engine vehicle, about 85% of the energy in the gas tank is essentially thrown away as heat. In an EV, 85% of what comes out of the wall socket goes straight to the wheels. However, the real issue that Wright hits on here is the scope for optimization around a core design.
“Any competently engineered EV is going to be similar in efficiency, but you can now optimize across a big scale,” says Wright. “So say we optimize one vehicle for 50hp and another for 1,000hp. We can do that because we have the batteries, we have the motors. It’s not a problem. And now that you’ve done that, take two otherwise identical vehicles, drive them on the combined cycle and see which one uses more energy. Chances are it’s the 50hp one.
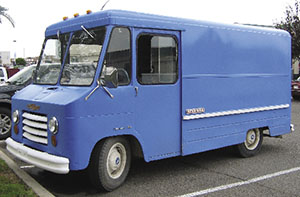
FIGURE 2 Ugly or not, step vans could be crucial for the EV market
“If you think about it, the one that’s engineered for the higher power is going to have lower impedance batteries, it’s gonna have thicker wires, it’s gonna have lower I2R losses in the motors. It might have higher switching losses in the inverter, but on balance it’s probably going to use that little bit less when you drive it to the EPA cycle, where you only need 30hp to 40hp. Yet for that car, you can put your foot down and you’ve got 1,000hp. That’s magic. That really changes things.”
In short, Wright is looking at coming at the market from two directions. “I know a few guys who drive the Bentleys and other big high-performance cars, and they’re a bit embarrassed at what they have and what it’s chugging down. But that market is also very open to new ideas, those drivers are looking for this kind of thing. Indeed, generally if you take our car around, people think it’s cool. There’s not that resistance to the fact that it’s an EV that I think I’d have expected a few years ago. And it’s the same with the guys already driving pick-up trucks. People will look at the options here.
“So this is going to be a surprise. You’re going to see EV coming from the high-performance end, and also from the high fuel consumption end. It’s not going to be the mainstream family cars to start with. In this example, if you’re building a supercar, you can also now approach the engineering by saying, ‘What top speed do I want?’ and then design the motor for a certain rpm; gear it for that top speed and just increase the power until you can do everything you want with just one gear. This is a very different world.”
In fact, the differences are not just in the best markets for the technology. The design approach is also fundamentally different to what has been seen in the automotive world before. If you look at a traditional vehicle, the effort and the intellectual property largely reside in the development, enhancement and refinement of the combustion engine.
“There’s a massive amount of black magic in the mechanical stuff, the shape of the CAM load, the materials used, the lubricants, the gas-flow dynamics,” says Wright. “When the torque feel of these cars doesn’t match what you need at the wheels, you have to dig down to yet another level of mechanical complexity to couple it. Or to put it another way—if you look at a company like Ferrari, what they do with the styling is incredible, but it still comes down to the engines and the transmissions.”
“When you think of all that, what we do is very different. We’ve got a high-speed, permanent, brushless magnet DC motor. There are two stages of epicyclic gear reduction. You couple that to the wheels, and you’ve got three ball bearings and a couple of gears—and basically, you’re done. There’s no transmission. So where’s the complexity now, where’s that IP?” says Wright. “Well, you’re moving all that from the mechanical stuff into the software and the electronics.”
There are lots of DSPs and general-purpose processors in there. There are complex waveforms to generate for the motors. There are sophisticated sensing systems to provide optimization and even energy harvesting—for example, there’s the potential to recover energy from the 2500hp that a 16,000lb truck can put into braking on a hard stop. And, there is safety to consider. All of this and more means that Wright and his team still have their work to do.
But there is one other factor that comes into play here. Because they are largely designing from the ground up, and not so inhibited by a century of prior innovation, Wright and his team can use a true system design approach.
“The existing car companies are really smart companies, and you can say that about Toyota or GM. But if you look at the design, first, yes, it is mechanically led, but second, it is also very incremental and very compartmentalized,” says Wright. “There’ll be one group of engineers working on the engine management systems and there will be another working on the stability control and so on. They’re systems, but they’re also black boxes.
“So, if you look at how a modern European luxury car works, you will hear a lot of talk about systems, but that’s about a set of black boxes inside and the wiring. You add and you add and when you’ve got something solved and in volume production, you don’t want to mess with it. So, rather than integrating things—which is what we look at doing if you take an electronics perspective—you look at hooking them together. It’s a different thing and it’s not as efficient. Though I can’t blame them for doing it like that—like I said, once you’ve got these things rolling off the production line, you get cautious.”
Also, the persistence of this design model may suit Wright well in the longer term. “I’m an optimist,” he says. “Within a decade, you’re gonna have electric motors driving wheels directly on more than 50% of cars. Now, for the family cars, it is going to be a long slog, but there are already some markets to aim for and that’s going to grow. Right now, though, for Detroit to be interested, you’ve got to be making probably more than 100,000 of these EVs a year—anything below isn’t of interest to them. They know what’s happening, but it’s not their business yet. But one day it will be.”
“When that happens, we’ll have the system experience for EVs, and what I’m hoping is that we can go to them and say, ‘Look, save yourselves a few years and few billion dollars’—and we license them the technology.”